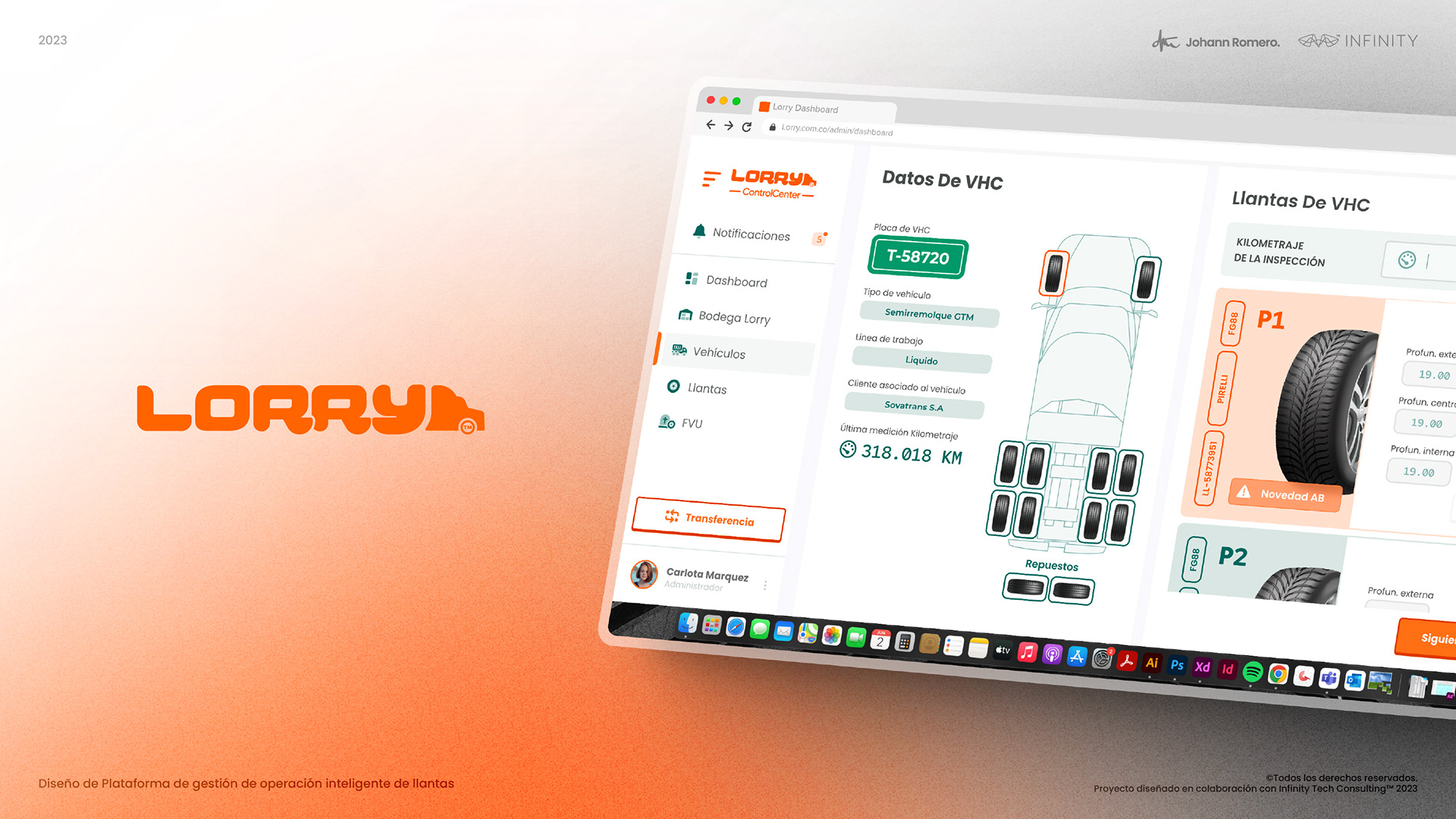
One of the drawbacks to solve was to manage a huge amount of tires in a clean software with a clear content tree that would allow the operation without any kind of friction between the different areas of the company. In this way, it would consolidate the optimization of processes that would represent more than $800,000 USD in profitability for the company.
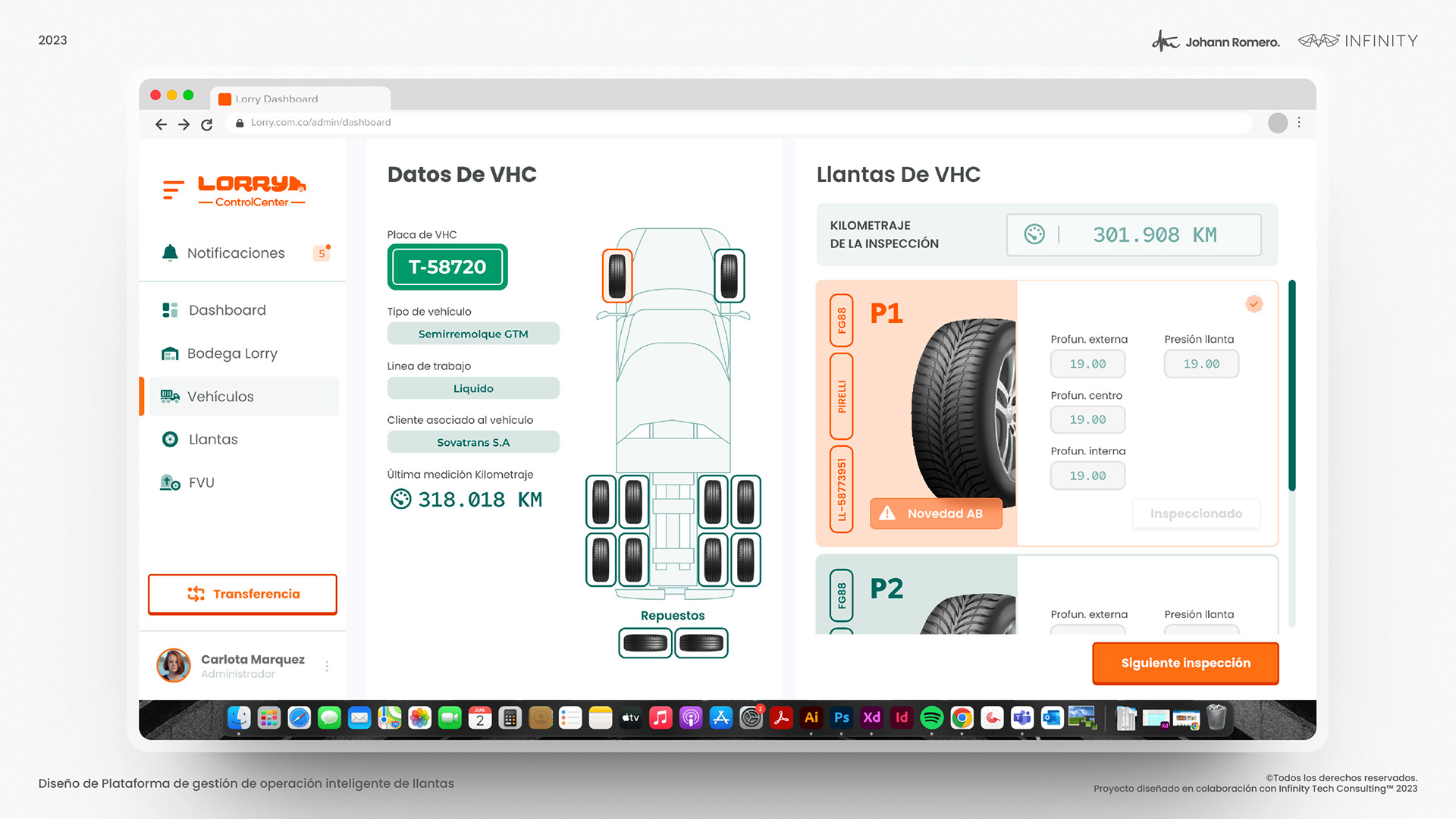
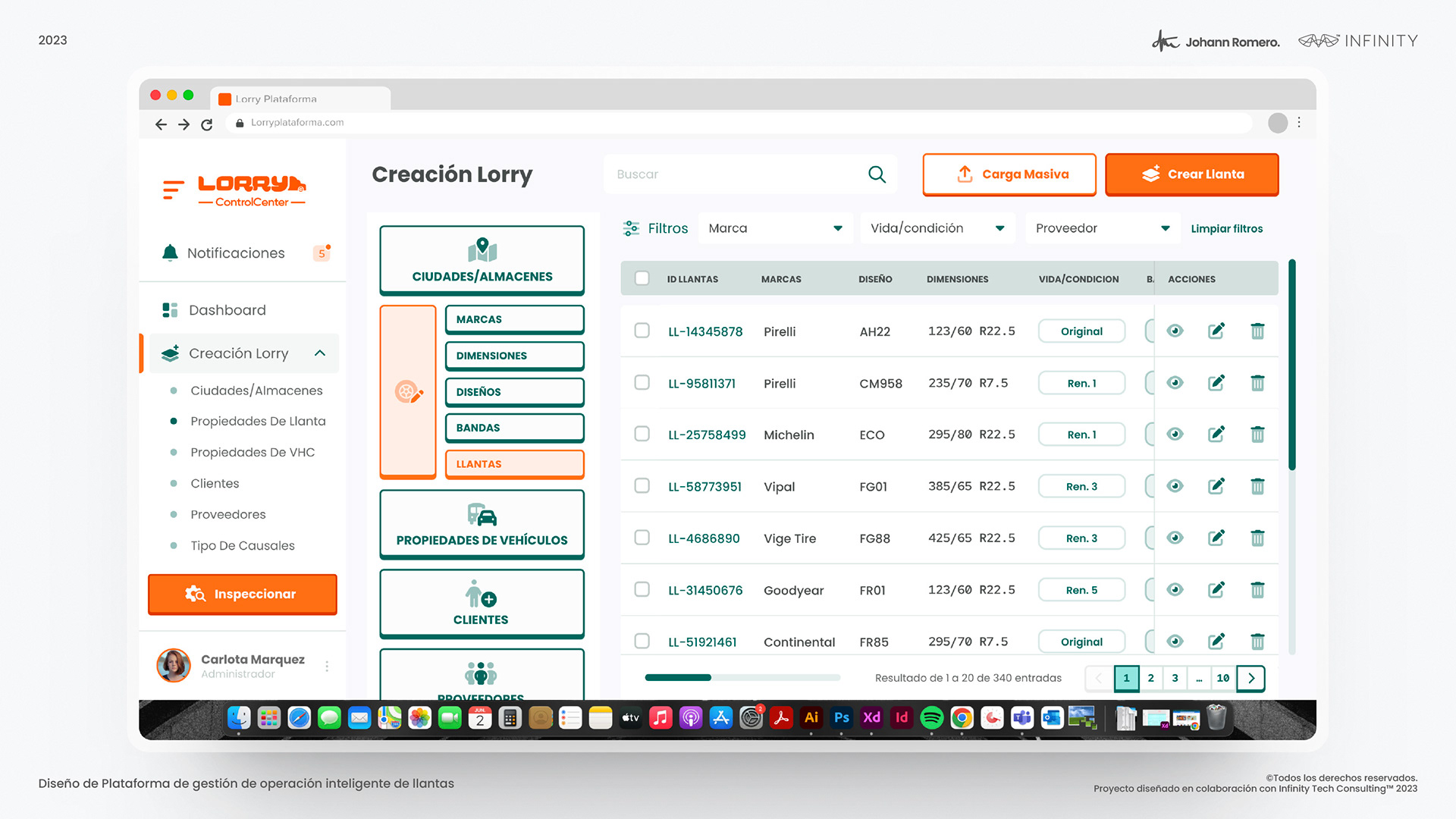
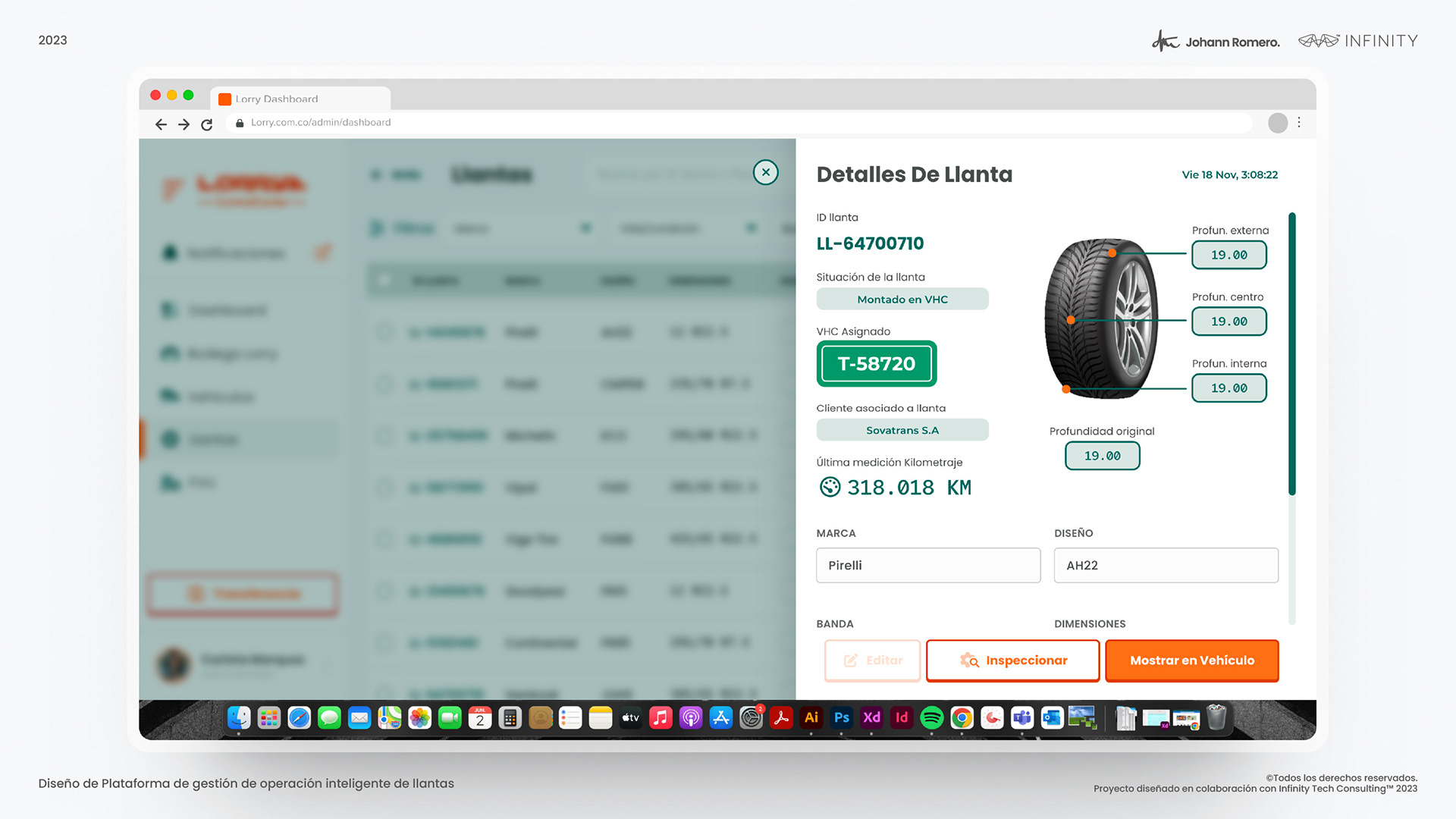
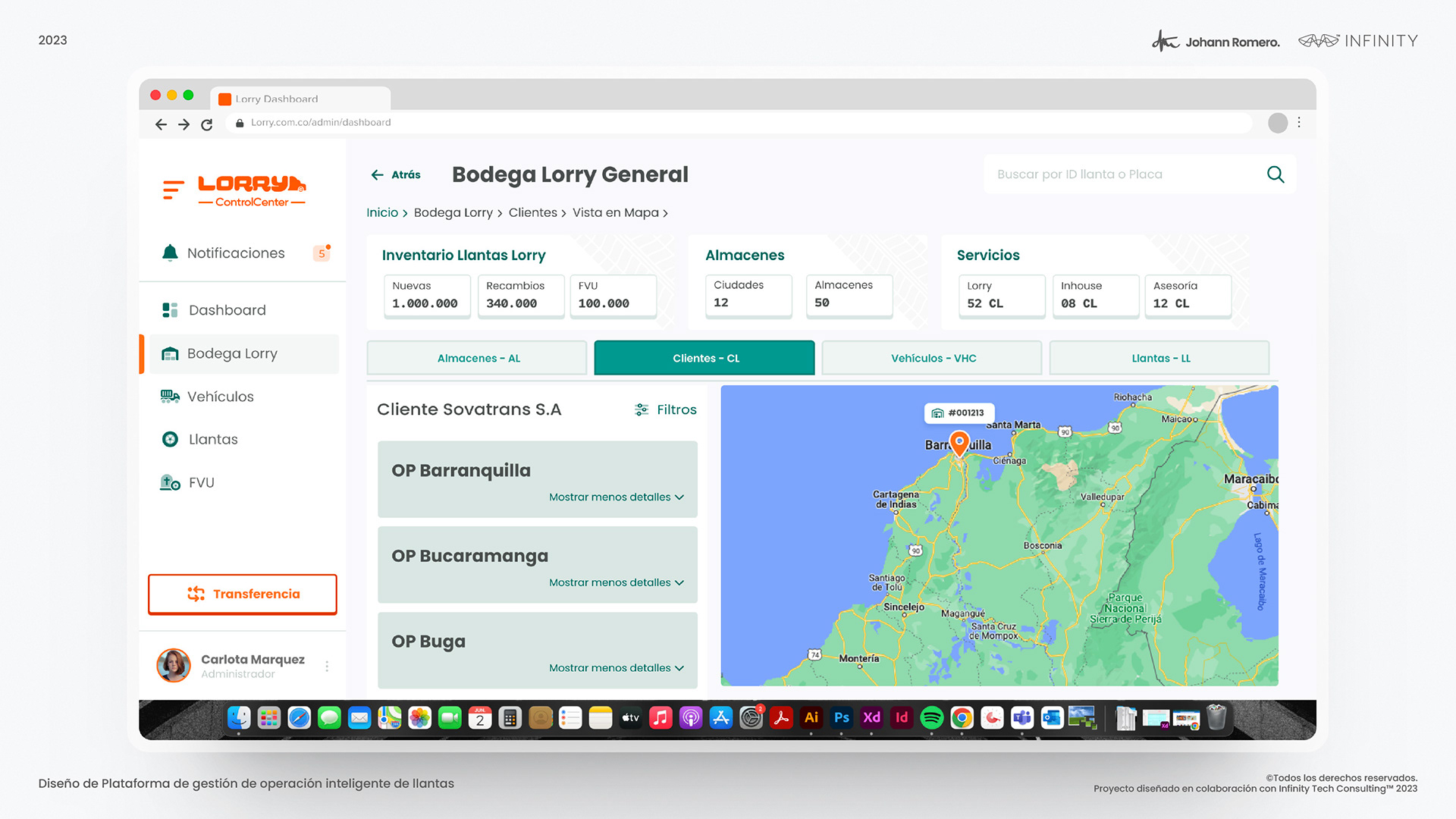
Achievements
Thanks to this project, we have been able to increase by 12% the speed in the management and evaluation of the condition of the tires at the time of their on-site evaluation.
We were also able to build an information architecture that would form the basis of the modular construction that was implemented for the subsequent creation and addition of new operational modules.
Through this experience I was able to condense again different practices and design methodologies in the construction of high performance design systems that manage to integrate successfully in a technological solution that has so many edges that it is perceived as a mega project in the medium-long term.
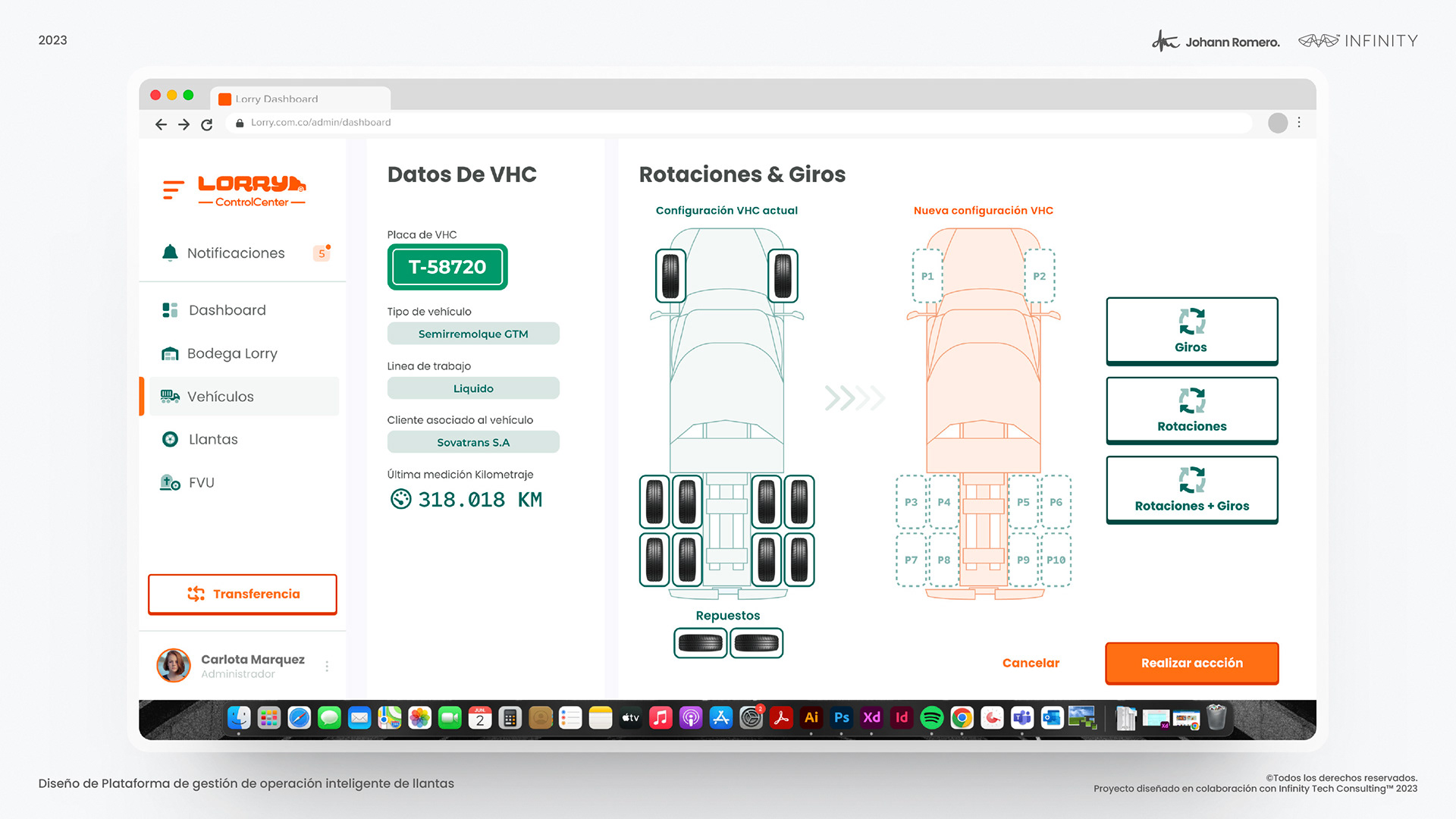
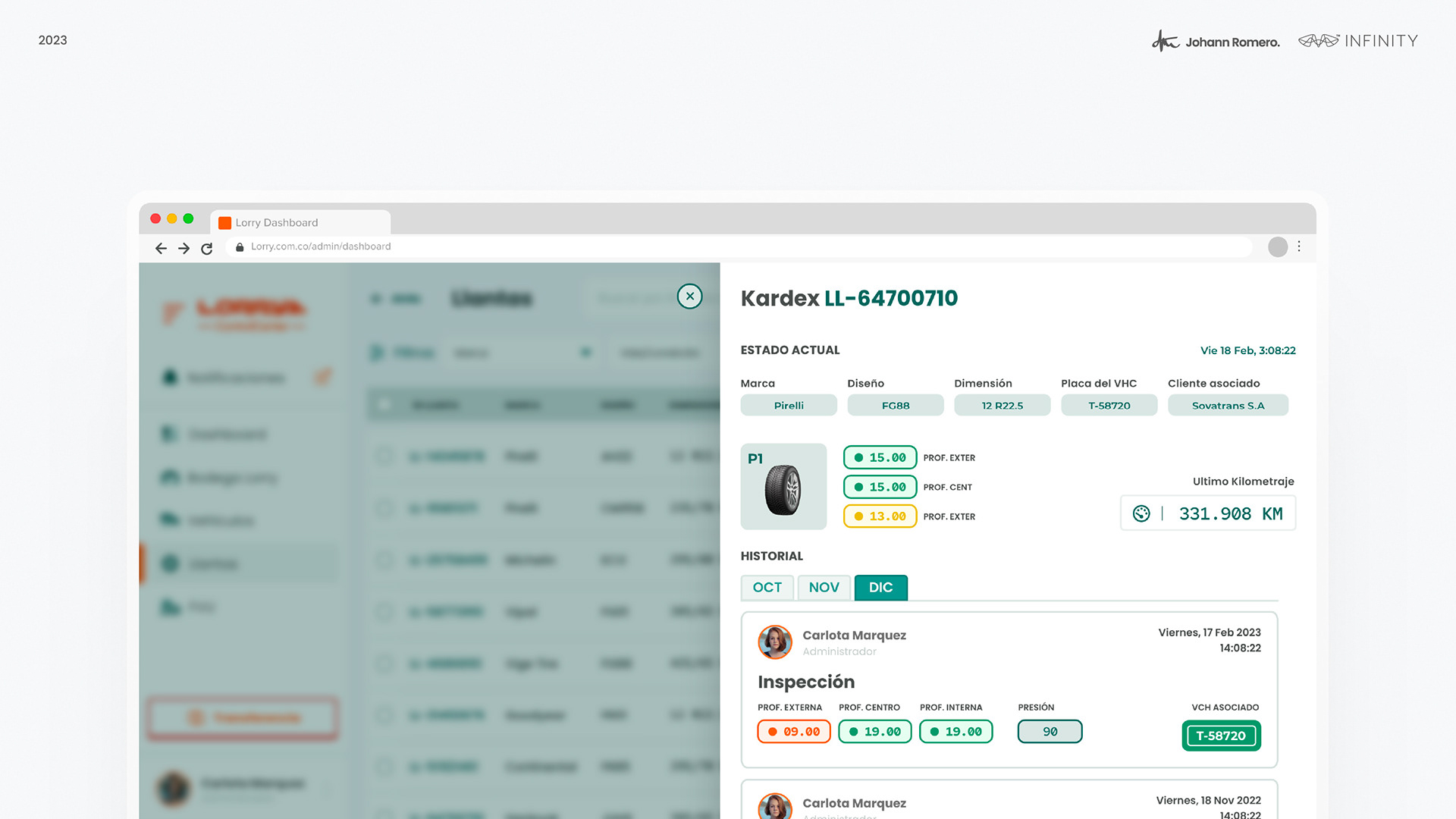
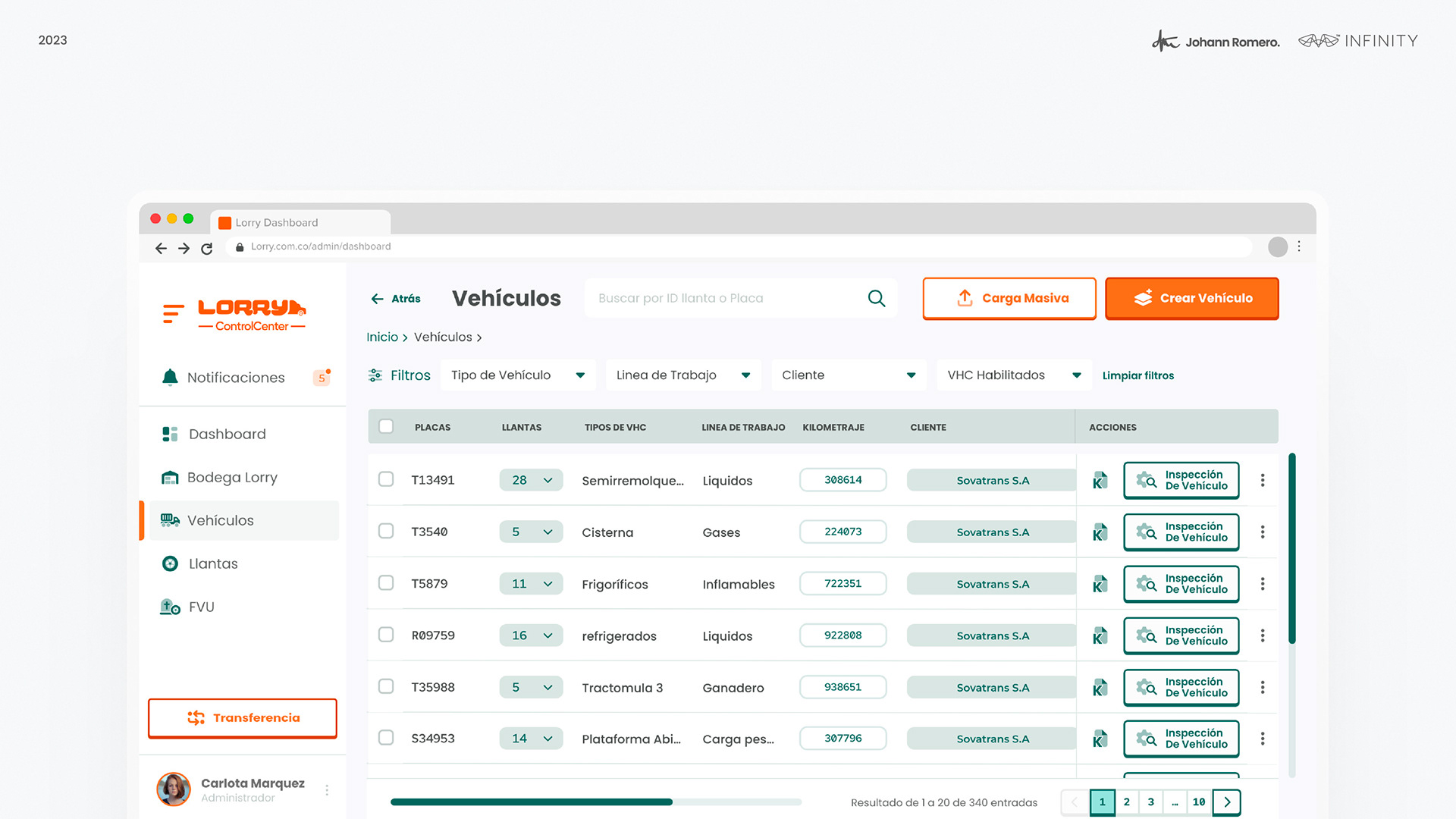
Lessons learned
During the design of the tire inventory management software, we learned that simplicity and clarity are critical. Users need to navigate the system intuitively and efficiently, especially in time-critical environments such as an auto repair shop. Incorporating a clean and functional interface, with quick search and filtering functions, allowed us to optimize the user experience and minimize the learning curve.
When designing the software, we realized the importance of creating a platform that can adapt to different types of businesses and inventory management models. This meant designing a modular and customizable system that can easily integrate with other existing systems, such as billing or customer management systems. Maintaining this flexibility allowed us to address the specific needs of each client and ensure a successful implementation of the software in a variety of business contexts.
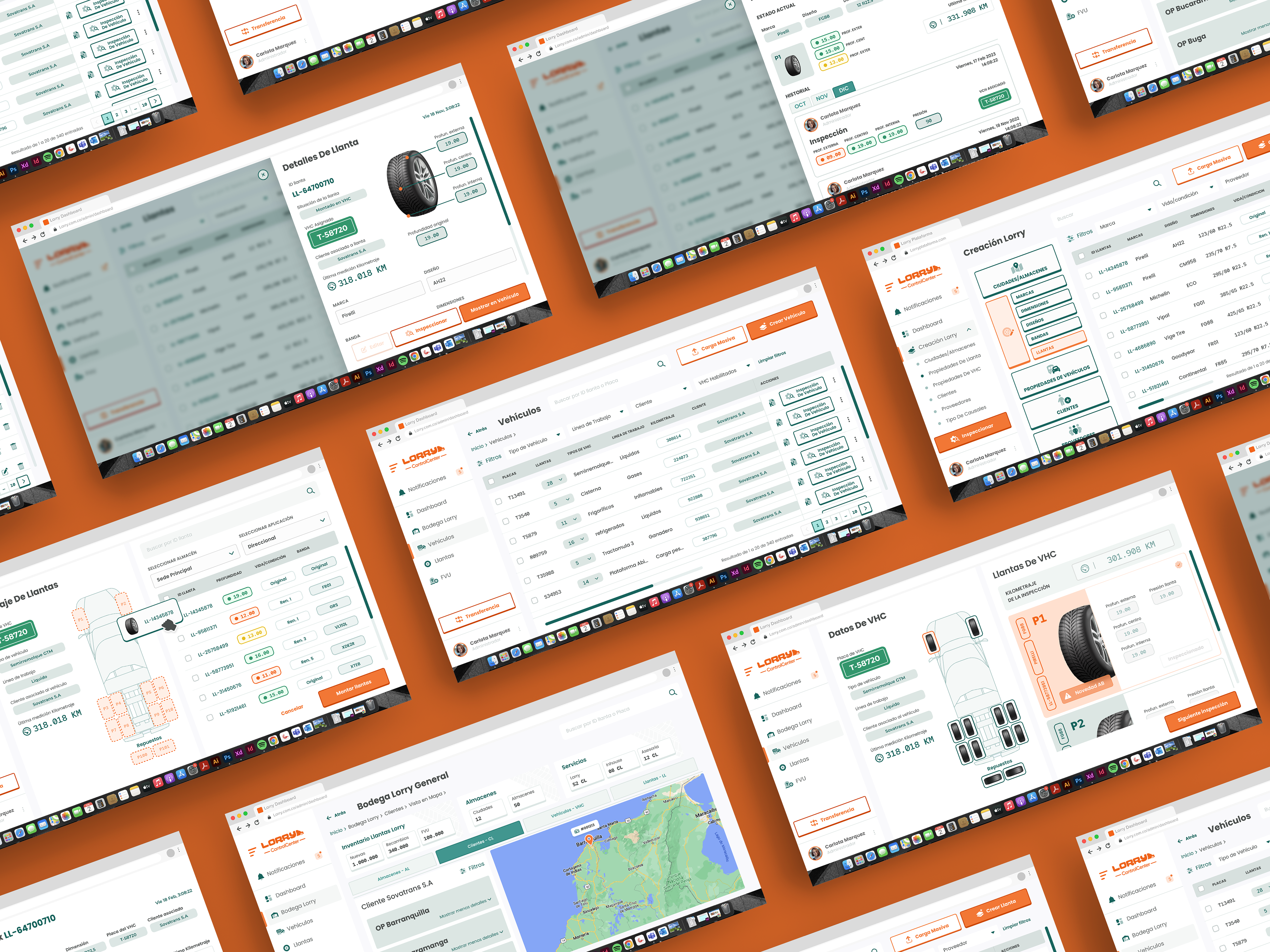